Introduction
A staggering 90% of industries rely on barcode scanners for inventory management and operational efficiency. Yet, the issues with industrial barcode scanners can significantly disrupt the workflow, leading to increased downtime and reduced productivity. From scanning errors to compatibility problems, these challenges not only affect the immediate task at hand but also have a ripple effect on supply chain management and customer satisfaction. In this post, we’ll delve into the common hurdles businesses face with these devices and offer practical solutions to overcome them. By understanding the intricacies of barcode scanner technology and implementing strategic fixes, companies can ensure smoother operations and bolster their bottom line.
Key Takeaways
- Industrial barcode scanners are crucial for efficient operations, but they can face various issues, from connectivity problems to software challenges.
- Identifying common issues early can prevent significant disruptions in workflow. Regular checks and understanding error messages are essential steps.
- Troubleshooting connection problems often starts with checking cables, Bluetooth, or Wi-Fi settings, ensuring your team can maintain productivity with minimal downtime.
- Enhancing scan performance may involve cleaning the scanner’s lens, adjusting the scanner’s settings, or upgrading the device firmware to improve accuracy and speed.
- Power and battery solutions are critical for uninterrupted operations. Implementing a charging schedule and using high-quality batteries can significantly reduce power-related issues.
- Addressing software challenges requires keeping the scanner’s software up to date and ensuring compatibility with your system, which can greatly enhance efficiency.
- Optimising scanner settings for your specific needs can lead to better performance. Customisation allows for a more streamlined scanning process tailored to your operation.
- Implementing preventive measures and best practices, such as regular maintenance and staff training, can significantly reduce the likelihood of encountering issues with industrial barcode scanners.
Understanding Industrial Barcode Scanners
Evolution of Technology
Over the past decade, barcode scanning technology has seen rapid advancements. Initially, industries relied heavily on 1D barcodes for basic data collection. The shift to 2D barcodes marked a significant milestone. These newer barcodes store more information and support complex applications.
The integration of AI and machine learning has further enhanced scan accuracy. They help scanners recognise damaged or poorly printed barcodes. This evolution has been crucial for industries that demand precision.
Key Benefits
The primary benefits of modern industrial barcode scanners are increased efficiency and data accuracy. By automating data capture, businesses reduce manual input and errors. This leads to significant cost savings.
Another major advantage is the ability to track products and inventory in real-time. This capability ensures better stock management and customer satisfaction. It highlights how technology can streamline operations across various sectors.
Common Uses
In retail, barcode scanners play a pivotal role at checkout points and in inventory management. They speed up transactions and help maintain accurate stock levels.
In logistics, these devices are essential for tracking shipments and managing warehouses efficiently. They ensure goods move smoothly from origin to destination without delays or losses.
Healthcare also benefits from barcode technology. It aids in patient identification and medication management, reducing the risk of errors significantly.
Identifying Common Issues
Scan Accuracy Problems
Issues with scan accuracy often stem from damaged or poorly printed barcodes. These imperfections can prevent scanners from reading the data correctly, leading to errors in inventory tracking and checkout processes. Furthermore, low contrast between the barcode and its background complicates the scanner’s ability to distinguish the code. Environmental factors, such as inadequate lighting, further exacerbate these issues. Bright sunlight or dim warehouse areas can make it difficult for scanners to accurately capture barcode information.
Slow Scan Rates
Outdated hardware significantly contributes to slow scan rates. As technology advances, older scanners struggle to process information as swiftly as newer models. This discrepancy results in longer waiting times and decreased productivity. Moreover, software not optimised for current barcode standards can hinder a scanner’s efficiency. The user’s technique also plays a crucial role; improper alignment or inconsistent scanning speeds can further slow down the process.
Unrecognised Barcodes
Frequent updates in barcode formats necessitate corresponding updates in scanner software. Without these updates, new barcode formats remain unrecognised, disrupting operations. Incorrect barcode formatting adds another layer of complexity, as it prevents scanners from interpreting the data correctly. Foreign substances like dirt or liquids covering part of the barcode can obstruct its recognition, leading to frustration and delays.
Device Interference
Electromagnetic interference poses a significant challenge in environments dense with electronic devices. This interference can disrupt scanner functionality, leading to inaccurate scans or complete failures. Other wireless devices operating on similar frequencies compound this issue by causing signal confusion. Physical obstructions between the scanner and its receiver impede wireless communication further, affecting both range and reliability.
Troubleshooting Connection Problems
Ensuring Proper Setup
Proper setup is crucial for industrial barcode scanners to function efficiently. Manufacturers provide guidelines that must be followed meticulously. These instructions ensure the device works as intended right from the start.
Correct positioning and alignment are vital. They enable the scanner to capture data accurately. This means placing the device where it can easily read barcodes without interference.
Configuring scanner settings is equally important. Each use case demands specific configurations. Failing to adjust these settings can lead to suboptimal performance or even non-functionality.
Resolving Connectivity Issues
Connectivity problems often stem from simple causes like distance limitations or obstacles in the environment. These factors can disrupt the signal between a barcode scanner and its base or connected system.
Troubleshooting steps should start with basic actions such as restarting devices and checking connections. Often, these simple measures can resolve issues quickly.
Ensuring compatible software and hardware is paramount. Mismatched components can cause persistent connectivity problems that are difficult to troubleshoot.
Enhancing Scan Performance
Cleaning for Accuracy
Regular maintenance is crucial for industrial barcode scanners. Dust and debris can significantly hinder their performance. It’s essential to clean the lenses frequently to ensure optimal functionality. Using recommended cleaning solutions and materials prevents damage and maintains clarity.
A clean scanning environment directly influences accuracy. It reduces the likelihood of misreads or failures, thus enhancing efficiency in operations.
Optimal Scanning Practices
Training users on proper scanning techniques is vital. The correct angle and distance between the scanner and barcode improve readability. Steady hands and a consistent pace during scanning also contribute to higher success rates.
Employing aiming guides or markers aids in achieving precise scans every time. This practice ensures that each scan is as effective as possible, reducing errors and saving time.
Software and Hardware Updates
Keeping scanner software and firmware up to date is non-negotiable. These updates often contain fixes for known issues, enhance security, and sometimes introduce new features that can improve scanning efficiency.
Upgrading outdated hardware can lead to significant improvements in performance and compatibility with newer systems. It addresses not just operational inefficiencies but also secures data processed by these devices against emerging threats.
Power and Battery Solutions
Troubleshooting Power Issues
Power-related issues in industrial barcode scanners can significantly hinder operations. Common problems include battery depletion and faulty chargers. These challenges not only affect scan performance but can also lead to unexpected downtime. It’s crucial to use manufacturer-recommended power sources to avoid these issues. Such sources ensure compatibility and prevent damage that third-party options might cause.
To conserve power, users should adjust screen brightness and sleep settings. These steps help extend battery life during long shifts. They also ensure scanners are ready for use when needed, maintaining operational efficiency.
Battery Management Tips
Proper battery charging practices are vital for extending the lifespan of industrial barcode scanners. Overcharging or using unsuitable chargers can reduce battery efficiency over time. To mitigate this, following the manufacturer’s guidelines on charging is essential.
Using power-saving modes and features benefits scanner longevity. These modes adjust the device’s operations, reducing energy consumption without compromising performance. This approach is particularly useful in environments where scanners are in constant use.
The importance of having spare batteries for critical operations cannot be overstated. Spare batteries ensure that devices remain operational throughout the workday, preventing delays in logistics or inventory management tasks. This preparation is a key component of effective battery management.
Addressing Software Challenges
Compatibility Solutions
Ensuring scanner compatibility with existing systems and software is crucial. It prevents operational hiccups. Many businesses face challenges when integrating older barcode scanners with new technology platforms. This mismatch can lead to inefficiencies.
One solution lies in the use of middleware or adapters. They bridge compatibility gaps effectively. Middleware serves as a translator between the scanner and the new system. Adapters, on the other hand, allow physical connectivity where it was previously impossible. Both options ensure seamless integration, maintaining operational flow.
Updating Scanner Software
Regular checks for software updates are essential for barcode scanners. They ensure devices operate efficiently and securely. The process involves connecting the scanner to a computer or network that can access the manufacturer’s update service.
Scheduling updates during off-peak hours minimises disruption to operations. It’s a strategic move to avoid downtime during critical business periods. Moreover, enrolling in automatic update programmes offered by manufacturers simplifies this process. It ensures that scanners receive timely updates without manual intervention, enhancing security and performance.
Optimising Scanner Settings
Checking Barcode Quality
Regular checks for barcode quality are vital. They ensure that barcodes meet industry standards and are easy to read. This process involves assessing both the physical condition and the compliance of the barcode against set guidelines.
Verification tools play a crucial role in this evaluation. They measure aspects such as contrast, edge definition, and overall readability. The outcome helps identify issues that could hinder scan success.
The impact of print quality cannot be overstated. Poor print quality directly affects scan success rates. It leads to delays and errors in data capture processes. Therefore, maintaining high print standards is essential for efficient operations.
Adjusting for Performance
Adjusting scanner settings is necessary for optimal performance. This adjustment accounts for varying environmental conditions and different types of barcodes encountered daily.
Custom profiles offer significant benefits in diverse scanning scenarios. They allow scanners to perform efficiently across a range of conditions, from low light environments to scanning reflective surfaces.
Feedback mechanisms, such as beeps or lights, are indispensable. They provide immediate confirmation of successful scans, enhancing operational efficiency. This feedback is particularly useful in noisy or visually obstructed environments where visual confirmation may not be possible.
Preventive Measures and Best Practises
Regular Maintenance Tips
Regular maintenance is not just a recommendation; it’s a necessity for keeping industrial barcode scanners in prime condition. Adhering to a maintenance schedule ensures that devices are cleaned and serviced regularly. This practice plays a pivotal role in extending the lifespan of these essential tools. Dust, debris, and everyday wear can significantly impact performance over time.
It’s also crucial to keep detailed records of all maintenance activities alongside any performance issues encountered. These records provide valuable insights into potential recurring problems or areas requiring special attention. They serve as a guide for future maintenance, helping to prevent minor issues from escalating into major breakdowns.
Training for Users
The effectiveness of an industrial barcode scanner relies heavily on the user’s ability to operate it efficiently. Comprehensive training programmes are fundamental in equipping end-users with the necessary skills and knowledge. Such programmes should cover not only basic operation but also troubleshooting and optimisation techniques related to scanner settings discussed previously.
Ongoing support and refresher courses offer additional benefits, ensuring users stay updated on new features or changes in operational procedures. They reinforce best practices and help in retaining critical knowledge over time.
User feedback plays an integral role in identifying training needs and improving scanning processes. It offers direct insight into real-world challenges faced by users, guiding the development of more effective training materials and operational strategies.
Final Remarks
Navigating the complexities of industrial barcode scanners doesn’t have to be a daunting task. With a clear understanding of common issues, from troubleshooting connection problems to optimising scanner settings, you’re now equipped to enhance scan performance and tackle power, battery, and software challenges head-on. Embracing preventive measures and best practices further ensures your operations remain seamless and efficient. This knowledge not only bolsters your operational efficiency but also positions you as a savvy player in managing technological assets within your industry.
As you move forward, consider this guide as your go-to resource for overcoming any hurdles with industrial barcode scanners. Your commitment to applying these insights and adopting a proactive approach will undoubtedly pay dividends in the smooth running of your operations. Don’t hesitate to dive deeper into each area discussed; mastery comes with continuous learning and application. Let’s keep pushing boundaries together.
Frequently Asked Questions
What are common issues with industrial barcode scanners?
Common issues include poor scan accuracy, connectivity problems, battery life concerns, software glitches, and suboptimal scanner settings. Addressing these can significantly improve performance.
How can I troubleshoot connectivity problems with my barcode scanner?
Start by checking the scanner’s wireless or cable connections. Ensure that the device is correctly paired or connected to your system. Resetting the connection often solves the issue.
What steps can I take to enhance my barcode scanner’s performance?
Regular maintenance, updating software, optimising scanner settings for your specific needs, and using high-quality barcodes can all enhance scan performance.
How do I address power and battery issues in barcode scanners?
Ensure your scanner is charged properly. Consider carrying spare batteries or investing in a model with longer battery life for uninterrupted usage.
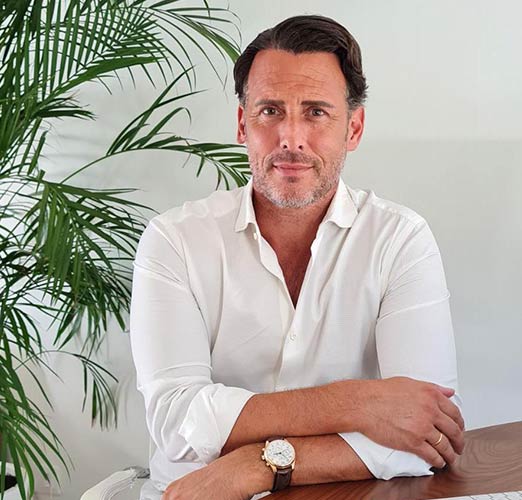
Ulrik Maxen: Specialist in rugged computers and mobile scanners
Ulrik is an industry veteran with over two decades of expertise working with rugged computers and mobile barcode scanners. Brands include Panasonic, DELL, Getac, Zebra, and Honeywell/Intermec. He is known for his commitment to delivering products and solutions that increase operational efficiency. Dedicated to following new market trends and client satisfaction, Ulrik is a trusted advisor where rugged computers and mobile barcode scanners must be deployed.